Moving from paper-based to digitized systems throughout the supply chain – from entry point to health facilities – provides better transparency around the movement of medicines and commodities in Zambia. This has been made possible by the Electronic Logistics Management Information System (eLMIS), a suite of software that manages health commodity supply chain data from the point of entry (central Level) to health facility commodity dispensation to clients (Facility Level). The USAID Electronic Supply Chain Management Information System (eSCMIS) project works closely with the Zambian Ministry of Health (MOH) to strengthen supply chain staff’s skills to improve data management, analysis, and forecasting using the eLMIS. Zambia’s digital supply chain transformation shows the significance of training supply chain managers with skills to install, administer, and oversee digital technologies.
The eSCMIS project uses on-the-job, in-person, and virtual training in addition to job aids and other tools to strengthen MOH staff capacity. Additionally, trained MOH staff are transferring skills to their colleagues to ensure sustainability while the project takes on a supportive role in preparation for full ownership of the system by the MOH.
From Super User to Champion: The Story of Lorent Kabamba
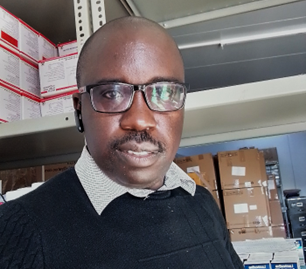
Lorent Kabamba, Pharmacy Technologist at Ndola District Health Office, Copperbelt Province.
Mastering the System
One cold Monday morning, I traveled to Misaka Health Post to roll out the eLMIS Facility Edition (FE)—a software that automates the day-to-day inventory management and dispensing of health commodities to patients. I was nervous because I only had two days to deploy and orient facility users -including the nurse managing the pharmacy who had no computer skills. Like many Zambians, she believes real work is only done on paper—computers are for playing games and music or watching movies. I decided to change the training method, starting with computer basics before moving to eLMIS system management. I ensured the training was hands-on.
My first task was to reassure the managing nurse. I showed her how to use the system and gave her practice tests. After a month of practice, the nurse was transferred to Zam-tan Clinic, a health facility also in kitwe. During one of my visits to Zam-tan Clinic, I found a nurse training other staff on how to use the eLMIS. The facility’s in-charge says the nurse is their IT technician. I was so proud of her achievements. I know she will soon be a master trainer – helping other health workers across the province. I am proud of her achievements and to be a part of her journey.
From Pilot to Adaptation
In 2014, I was invited to the first MOH eLMIS FE pilot training. Solwezi was our training ground for system use and deployment. The eLMIS FE pilot was still in its infancy and needed testing to emulate the Zambian supply chain. Despite the slow adoption of the system, I was excited about the process because we were developing a better supply chain system that was automated and more efficient than the manual paper-based supply chain system.
Practice Makes Perfect
In 2016, I spent time with a Systems Implementation officer who was in the Copperbelt to deploy and provide technical support for eLMIS. In Kitwe, she spent a day showing me how to use the system and how to provide technical support. I became familiar with the system and spent the rest of my time practicing. From May 2016 to November 2017, I spent three days in the office and two in the field, learning at high-volume facilities so I could provide technical support to other facilities in the province. I needed to understand what users go through daily while using the system. I put in enough practice that now I can conduct a user orientation over the phone and know exactly where features are no matter what page the user is on. Upon the release of a new update, I work in the field to keep up with the latest features.
Moving forward
During my time, I participated in over 28 deployments of the eLMIS and trained over 100 MOH staff. I am always in the field providing technical support and supervision and have helped over 170 facilities. I am now Copperbelt’s technical lead. I like strengthening other MOH staff’s capacity in digital supply chain management and contributing to their success. As we move towards ownership, I urge continued support from the project for MOH staff to provide comprehensive technical support and supervision.
“Of course, I was scared at first because I did not know how to use a computer before Mr. Kabamba showed me how. Now, I really appreciate the system. Before I even knew there was an eLMIS, I had to do paper reports for over a hundred products, and calculating consumption manually took a long time. Since my orientation with Mr. Kabamba, I have moved from Misaka Health Post to Zam-tan Clinic and back to Misaka Health Post. I’m still an eLMIS student, but I’m much more confident now, and I’m happy to help and teach anyone who wants to learn.”
Sharon Chikamba, nurse at Misaka Health Post, Ndola, Copperbelt Province.
All Hands-on Deck: The Story of Kazungo Kawengo
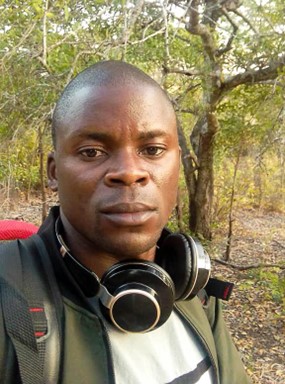
Kazungo Kawengo, Certified Daily Employee at Kaaba Rural Health Centre in Kaoma district, Western province.
From childhood, we are taught to help others in our tight-knit community. I knew it would be a tedious journey, walking three hours each way and crossing a wide stream to help our neighbor Kasabi Rural Health Centre get oriented with the eLMIS, but it did not sit right with me that we were progressing while they were left behind.
I am Kazungo Kawengo, a certified daily employee (CDE) at Kaaba Rural Health Centre in Kaoma District, Western Province. I grew up in Kaaba, and I know the area well. When I first started at the Kaaba Rural Health Centre, I was a security officer. As you know, Zambia’s rural facilities are understaffed. I always offered my services when needed, and the in-charge and other facility staff were eager to teach me, so I essentially became an assistant to facility staff.
I was excited when the MOH introduced the eLMIS. I had previously helped staff with paperwork reporting, which was tedious. We were all motivated to learn how to use the electronic supply chain system that would automate commodity management and reordering. Two months later, I was familiar with eLMIS. It is automated and user-friendly. eLMIS significantly reduces the wait time for our clients – under 5 minutes compared to over 10 minutes when we did paper-based documentation. The system helped us – especially knowing all our transactions and records were saved securely on the eLMIS system.
All provincial health facilities with eLMIS FE are connected to a 3040 WhatsApp Group where users send queries and receive regular eLMIS updates or feedback. When one of our hard-to-reach partner health facilities, the Kasabi Rural Health Centre, lagged behind with their reporting. My facility in-charge linked me up with the center and I offered to help. It was a three-hour walk, but I was determined to bring them up to speed with their reporting.
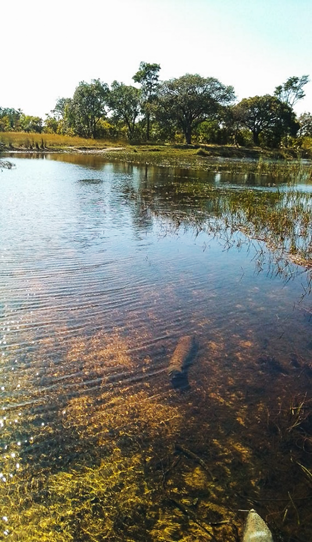
Lukute Stream, Kaaba, Kaoma district, Western Province
The in-charge at Kasabi and CDE warmly welcomed me. I showed them how to dispense medications, perform physical counts, update stock control cards, and submit a report to order medications. After we finished, we had to find a spot with good network, so I could show them how to send in their reports.
I encouraged Kasabi’s staff to practice using this system. Embracing work and engaging with an open mind makes it easy to learn. Since our initial training, I have visited the facility twice to check their progress. As a result, I am confident their reporting rates will rise.
“We really needed the orientation, and we appreciate Mr. Kawengo making the effort to come to our small facility. It is not an easy journey from Kaaba, and he made the entire journey on foot. Unfortunately, our system had not been updated when he arrived, so he could not walk us through all the new features. But he has made it a point to check in on us, and he has returned twice to ensure that we are making progress and that he can continue to carry us through the orientation. We are constantly practicing and learning new things.”
Martin Chinoya, Certified Daily Employee at Kasabi Rural Health Centre, Kaoma district, Western Province
Site Initiation: The Story of Cindy Chishimba
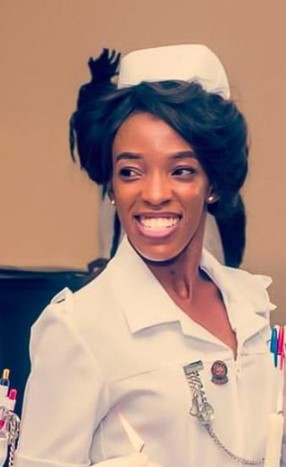
Cindy Chishimba, Nurse at Wusakile Urban Clinic in Kitwe, Copperbelt Province.
With the eLMIS, restocking a facility with medication is straightforward. Without it, we rely on less-accurate monthly paper reports for facility transaction details and must wait for someone to order medications using supply vouchers at the District Health Office. With the system, district and provincial supervisors can easily see your stock status and approve reorders in time for restocking. I had used the eLMIS for a while and was surprised to discover it was neglected when I moved to my facility.
My name is Cindy Chishimba, and I am a nurse at Kitwe’s Wusakile Urban Clinic in the Copperbelt. Unfortunately, our facility lacks a pharmacist, which is typical of small health centers.
I first discovered this as a norm in Luanshya at Kapenda Health Post. I did not intend to be a jack-of-all-trades, but in a small facility, you realize quickly that you are capable of more than you know. As a result, I found myself working alone sometimes and had to be a clinician, nurse, and pharmacist all rolled into one.
This was when my interest in pharmacy work grew. I observed the importance of being meticulous with medications – their utilization, recording what is dispensed, and how to submit reports on commodity stock levels. Here, I learned how laborious paper-based transactions are. Imagine my excitement when I found a better way to run a pharmacy at my second job posting when I moved to Allessandros Urban Health Center, also in Luanshya.
I was amazed by how quickly the pharmacy in-charge did his duties using the system. I would spend my breaks in the pharmacy asking questions and doing assignments to learn as much as possible. When I moved to the Mikomfwa Urban Health Center (Luanshya), I found we did not have many staff members who could use the eLMIS. This is where I got all my practice. I volunteered to work at the pharmacy, where I would conduct daily transactions. When I ran into trouble, I would call my colleague from Allessandros Urban Health Center, who was always willing to help and guide me through anything. Soon I was managing the entire pharmacy and utilizing eLMIS to run reports.
My fourth relocation is the one that brought me to the Wusakile Urban Clinic in Kitwe. When I discovered the eLMIS packed and unused, I had to play it cool for a while and study how things were done at the facility before applying my skill set. I consulted my boss about the eLMIS. He told me the pharmacist who knew how to use it had transferred to another facility, and other staff did not know much about it. I informed him of its benefits and that I understood how to use it. My boss was delighted at the prospect of me managing the eLMIS because he had been looking into acquiring assistance and orientation so the facility could start using the system again. I powered up the server and client machines and began working through the system. I found it required software and backlog updates before it could fully function. I contacted the project’s helpdesk and, with the support officer’s help, updated the system and cleared the backlog. It took some doing, but the system is now running.
Because I will not always be there, I started orienting other staff members on the system. We also embedded it in our work plan to have staff rotations on the system, so everyone has hands-on experience with the eLMIS. People learn how to use the system faster by making the orientations practical. As a result, two different nurses swiftly learned how to handle the pharmacy with eLMIS, and the antiretroviral therapy department is learning how to conduct its transactions with the system.
Papers are unreliable, ink fades, and that is no way to keep records. However, when you conduct stock management digitally, every transaction, even from previous years, is available with just a click of a button. I encourage my co-workers to learn, and I am glad we have a system that simplifies our work.
“So far, Cindy is one of two people I’ve been able to orient. It is a joy for me to teach others because I find that when I take the time to teach, I learn more. Cindy was a quick study. It is encouraging to see how far she has come. I remember when she moved to Mikonfwa and would call me for advice on things she did not know, but as time passed, the calls became fewer, and I realized she was becoming a pro. I’m glad to see she’s now passing on her knowledge to her coworkers.”
John Maimba, pharmacy in-charge at Mikonfwa Health Centre, Luanshya district, Copperbelt Province
The eSCMIS Project
The Electronic Supply Chain Management Information System (eSCMIS) project is funded by the U.S. Agency for International Development (USAID) and the U.S. President’s Emergency Plan for AIDS Relief. The project works with the MOH, Zambia Medicines and Medical Supplies Agency (ZAMMSA), Churches Health Association of Zambia (CHAZ), and other key supply chain partners to implement the eLMIS. This state-of-the-art, open-source digital platform provides end-to-end, real-time data.
Zambia is improving supply chain management by using digital tools. Digital skills add efficiency to health human resource routines. All healthcare cadres can contribute to supply chain management with training and tools. Over 4000 MOH staff received in-service training to improve supply chain management between January 2020 and June 2022. Training was customized for each function/cadre (e.g., IT (10), Data Entry/Management). Training included (53) Biomedical science staff (186), Pharmacy staff (244), Counselors (588), Nurses (736), Clinicians (167), etc. MOH staff deployed 215 of 673 facilities between January 2020 and June 2022. Simplified digital tools are a missing link to optimizing Supply chain management.