The implementation of the Zambian Ministry of Health’s (MOH) electronic Logistics Management Information System (eLMIS) – a digital supply chain management tool – by the USAID Electronic Supply Chain Management Information System (eSCMIS) project has involved a lot of activities and processes. Through various activities, the USAID eSCMIS project has continued to transform the eLMIS system into a platform that supports improved decision-making, accountability, fiscal responsibility, and local ownership, leading to a more efficient and sustainable supply chain, a more effective health system, and better health outcomes. Part of this process has been a series of system enhancements that have allowed for improved system performance and new functionalities and features. The project has, to date, completed and deployed 206 (85%) of 243 system enhancements requested by the Government of the Republic of Zambia (GRZ) based on user feedback, some of which include data analytics and visualization.
The availability of data analytics in the eLMIS system has been one of the most impactful results of the system enhancements since analytics are an important source of information for making data-based decisions. Here are some of the data analytics available in the eLMIS system and why they are helpful.
Stock availability status by location: This shows the percentage of reported stock available by location such as essential medicines and laboratory commodities. This feature assists supply chain managers in identifying locations with low and high stock and then determining appropriate redistribution measures.
Happy Zulu, Laboratory District Coordinator, Limulunga District shares that, “with the stock status data provided by the system, I am able to determine how much stock each of the facilities in the district needs. This ensures accuracy in distribution of stock and we can prevent stock imbalances (overstocking, understocking and stockouts) that can result from stocking decisions that are not data-based.”
“Using this information I can tell which facilities are about to be stocked out. This guides my decisions on which facilities to prioritize when we receive commodities,” added Lombe Mushintampanga, District Coordinator, Mpulungu District Hospital.
Stock availability trend: This shows the percentage of stock availability over a period of time and predicts future stock needs.
“We use this data to monitor the consumption levels of facilities and to determine how much stock the facilities under our district need. This helps us make decisions such as making an emergency stock order when the trend shows that the stock will run out before the district is restocked. Being able to determine a change in consumption trends helps us take proactive action, for example ordering less for facilities with low consumption trends or ordering more for facilities with high consumption trends. By doing so, we can prevent wastage and prevent situations where facilities are stocked out before the next date of restocking,” says Happy Zulu.
Stock imbalance: This shows stock percentages of commodities not stocked according to plan. This means overstocked, understocked, and stocked out and helps ensure that stock is not going to waste.
Lombe shares that, “When a facility is overstocked, the district retrieves the excess products and redistributes them to other facilities that are stocked out or have higher demand for the particular product(s).”
Percentage of waste report: By inputting the batch and expiry dates for all products managed using eLMIS, system users can track and trace any product in case of expiration, recall by MOH or manufacturer due to quality concerns, or discontinuation of use. The system is used to record damaged products that are considered unusable. All waste products are reported using this feature.
Happy explains that, “We are able to hide expired products in the system and monitor losses. However, the system starts flagging products that will expire six months ahead, so this has helped us have very few expiries/losses because we take action as soon as the system notifies us. The products are redistributed to facilities with higher demand.”
On-time delivery: The national logistics systems are designed to ensure products are made available to the client at the right time, with the right quality, delivered to the right place, at a reasonable cost, in the required quantity, and at the right time. eLMIS provides the capability to track the order from when the requisition is approved to when commodities are received at the health facility.
Report and requisition (R&R) passed the data quality check: The basis of resupply is dependent on the accuracy of the data captured and reported in eLMIS by the health facility. The national logistics system standard operating procedure (SOP) requires that a review of the data quality be undertaken at every supervisory level before approval for the next stage of the process. eLMIS has an in-built feature that assists the reviewer by holding the data that requires correction. This helps the supervisors save time by addressing the highlighted data.
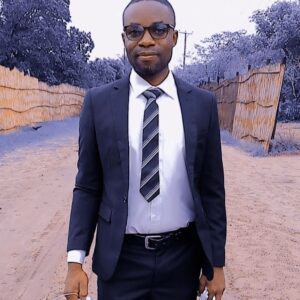
Happy Zulu, Laboratory District Coordinator, Limulunga District
“You would find that you give a facility 500 HIV test kits, which are supposed to last for three months, but they request for more after a month. This makes me question the quality of the data if indeed they used up all the test kits within the month. If they request for less than their monthly consumption trend however, it makes me question why they are requesting for less than what they normally use,” narrates Happy Zulu. He adds that, “When we follow-up on these issues, we usually find that this is as a result of poor documentation – where some data is omitted or not entered in the system. For example, a facility indicating that they still have the product when in actuality they have run out. This happens when consumption is not accurately recorded.” This can also help to prevent pilferage of commodities.
Reporting timeliness: This feature tracks health facility staff adherence to the SOP submission deadlines. Supervisors use this information to target facilities that submit reports late, establish the root causes, and implement remedial measures.
“When the system highlights facilities that do not report on time, I follow up to check if they have any challenges. Issues usually include system failure, network issues, and facility staff (especially new staff) needing orientation because they do not fully understand the system,” shares Lombe.
Happy adds that, “Besides following up I also ensure that facilities are reminded of the importance of observing the reporting time. We have a rider that we use to go to facilities when they have network issues to pick up their laptops for DHO to submit the report for them. The data can be entered while offline so DHO simply clicks the submit button once the facility laptop is connected to the internet.”
Trend of regular orders submitted per month: Using this analytics report, the supervisor has visibility into monthly submission trends, which helps to focus on low submission months, take further steps to establish the reasons and develop an action plan. For instance, an important factor such as the onset of the rains, does have an impact on commodity availability as facilities get cut off due to flooding and impassable roads. With this infographic, supervisors are now able to plan ahead in anticipation of such a challenge.